
Automated quality control in the paint shop
Streamline the paint shop quality assurance process by creating a singular, visual source of information and analysis.
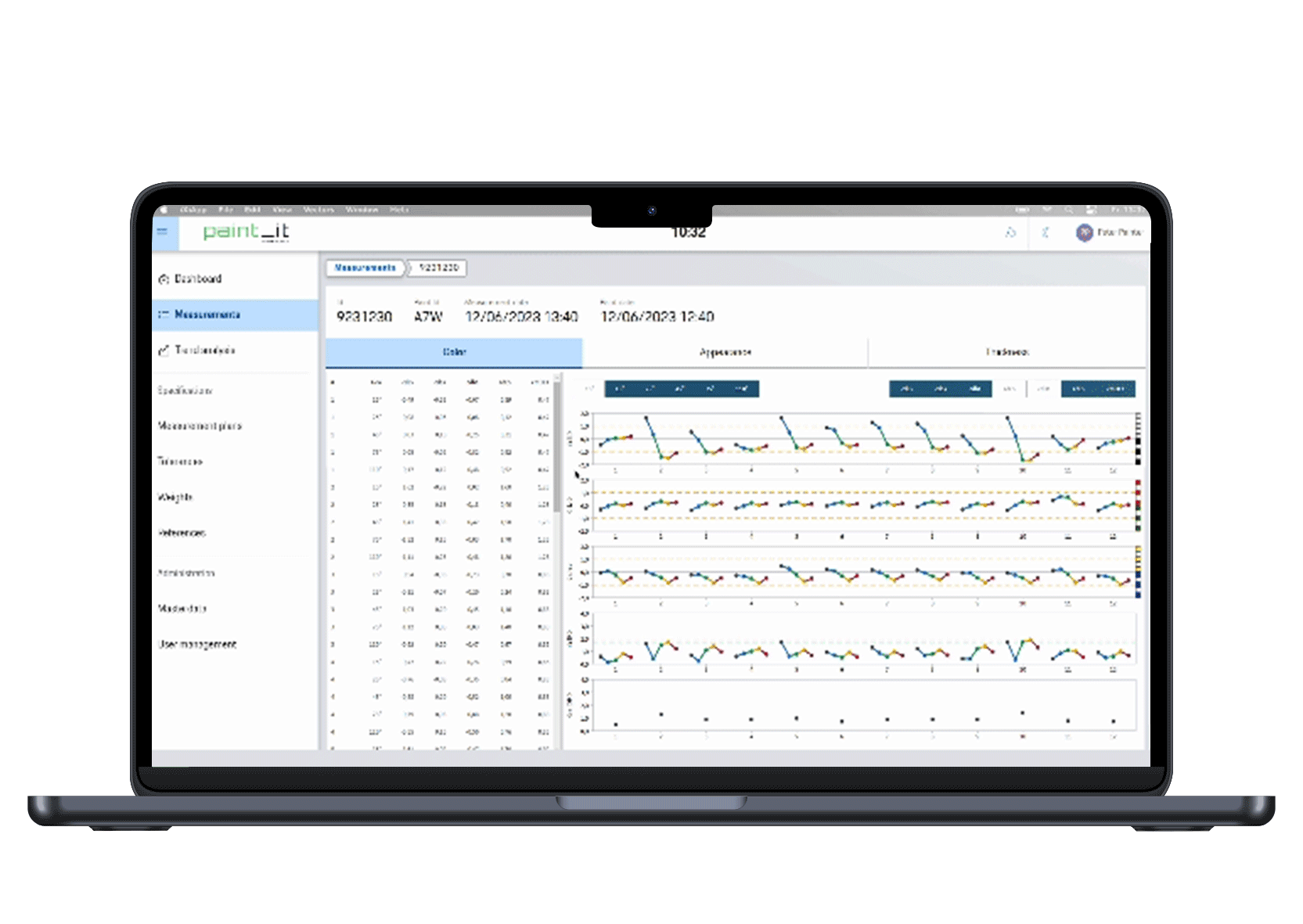
Our Customers
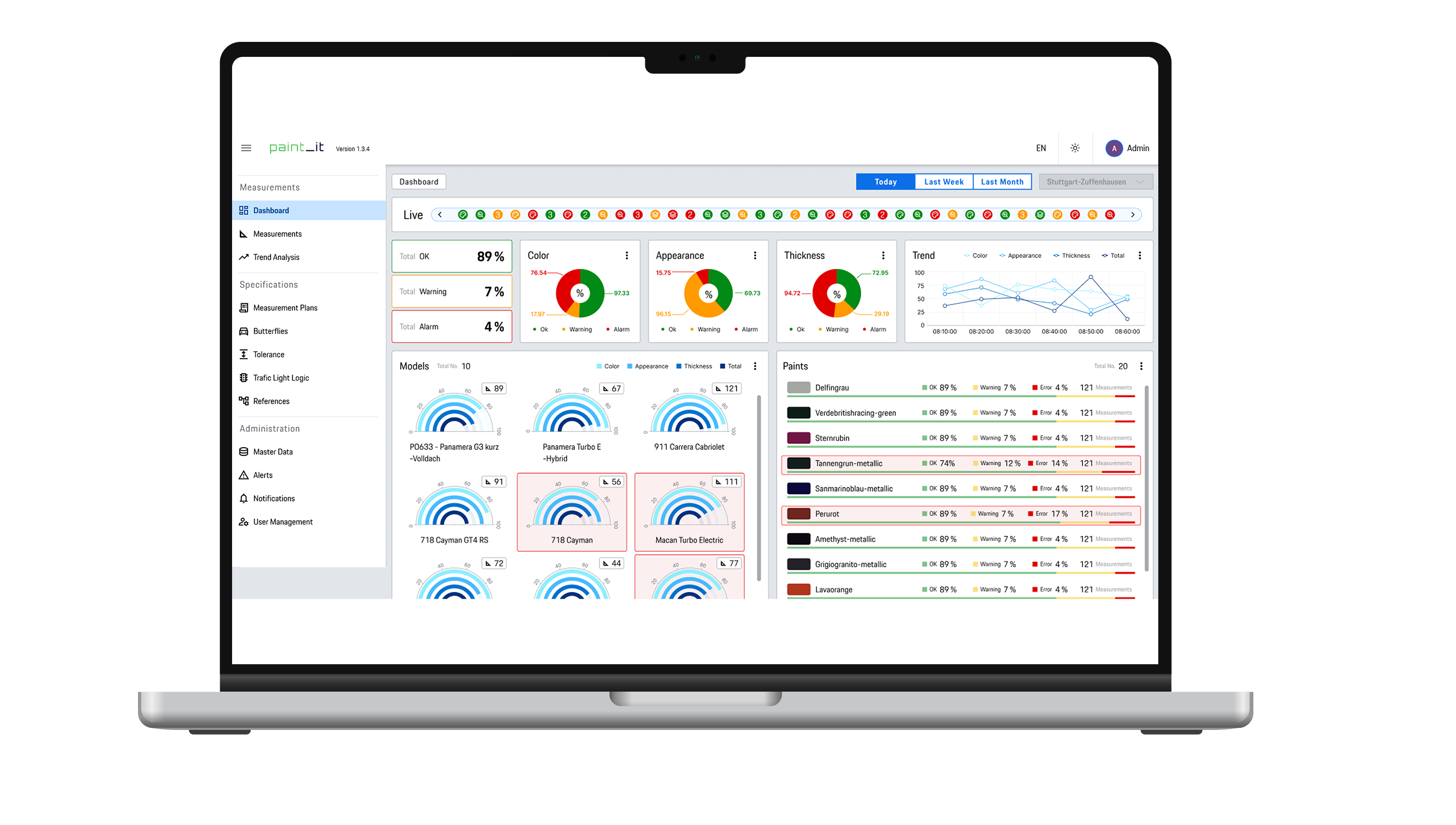
Automate Quality Inspection in the Paint Shop
Optimize your quality control in the Paint Shop with automated data collection and analysis. Automate the collection of measurement data for layer thickness, color, and appearance, and obtain a centralized database for meaningful analyses.
paint_it offers you an innovative software service solution that streamlines quality control in the Paint Shop.
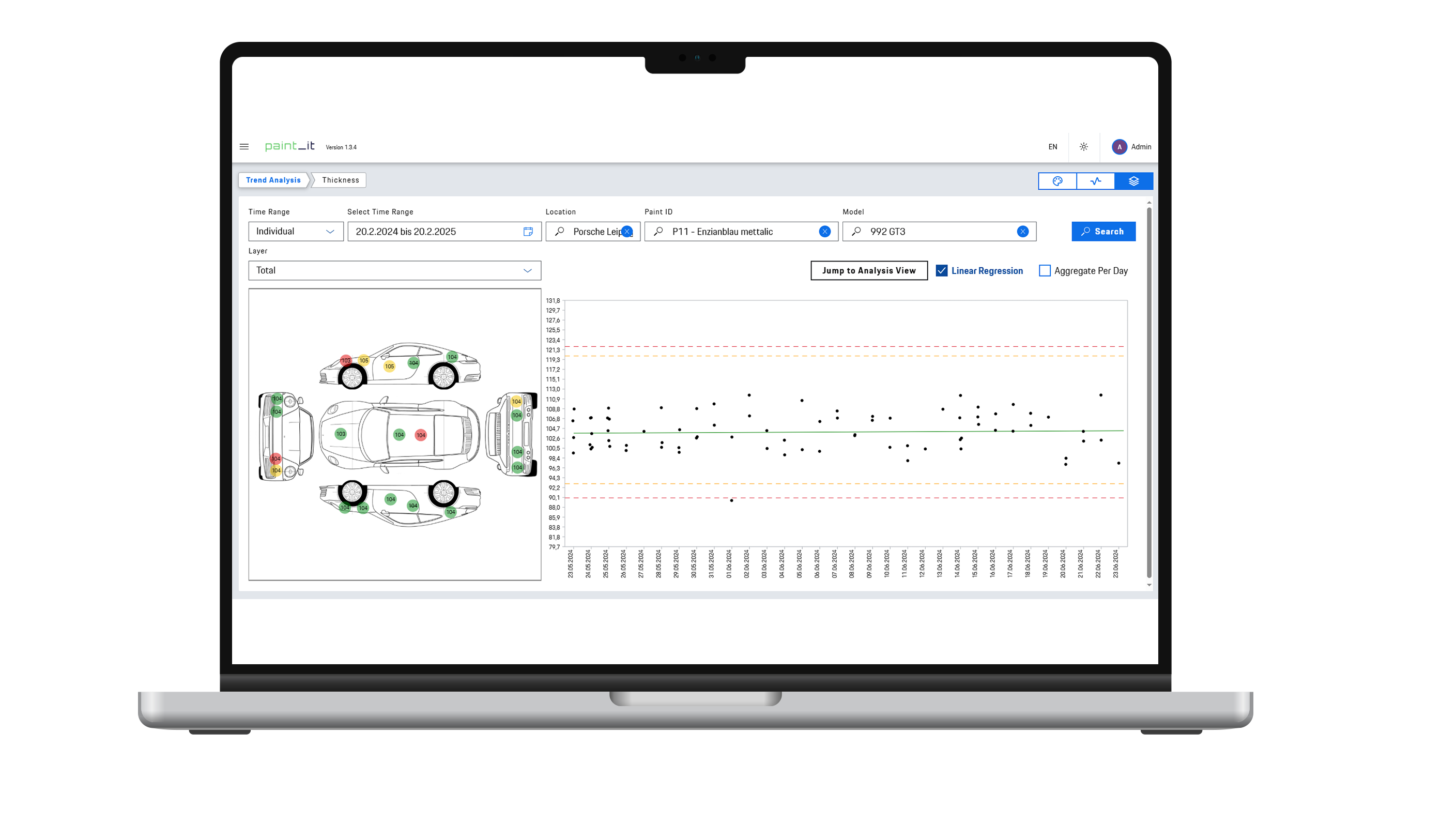
Anticipate Quality Deficiencies Early with Intelligent Data Analysis
With paint_it, quality deficiencies in painting can be detected not only within a short period but also to some extent predicted.
The system identifies trends and uses this ability to forecast increasing deviations of individual quality criteria from allowable tolerance values.
This allows timely countermeasures to be taken in the upstream processes.
Automated Quality Control
paint_it automates the collection, consolidation, and analysis of measurement data for layer thickness, color, and appearance. This makes quality control more efficient and reliable.
Reduced Costs
Lower material and energy costs by applying thinner paint layers. Additionally, achieve positive sustainability effects through reduced water consumption and CO2 emissions.
Centralized Database
Obtain a centralized database where all measurement data for quality parameters is stored. This enables meaningful analyses and continuous improvement of the painting process.
Features and functions
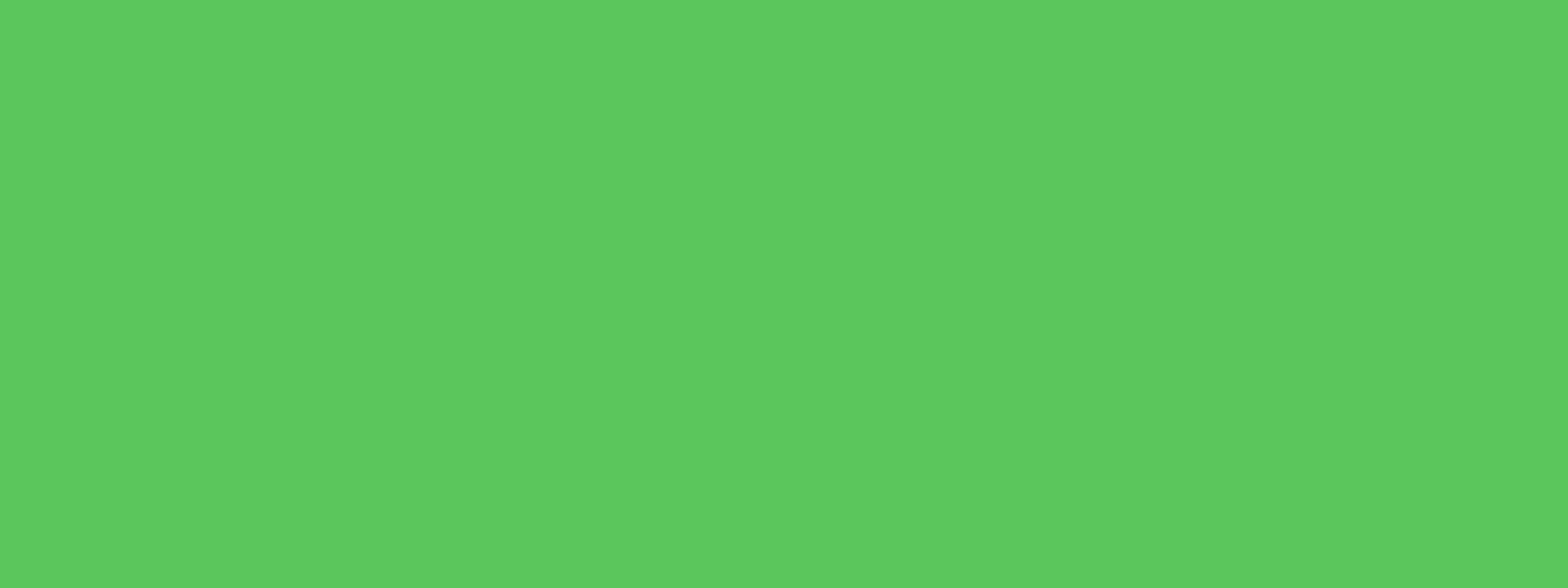
Optimized Quality Control Read More
paint_it compares the actual data captured by the measuring instruments with the target data. Deviations trigger immediate alerts, allowing affected bodywork to be repainted. Additionally, paint_it is fully compatible with a wide range of measurement devices and sensor systems, providing our customers with maximum flexibility and control over their workflows.
Trend Analyses and Heat Maps
Based on the measurement data, trend analyses can be conducted, and heat maps of critical parts of a body can be created. This provides insights into the painting process and allows for adjustments if necessary.
Cross-Location Optimizations
The data stored in the cloud enables cross-location access to best practices, facilitating cross-location optimizations in the painting process.
paint_it explained
Use Cases
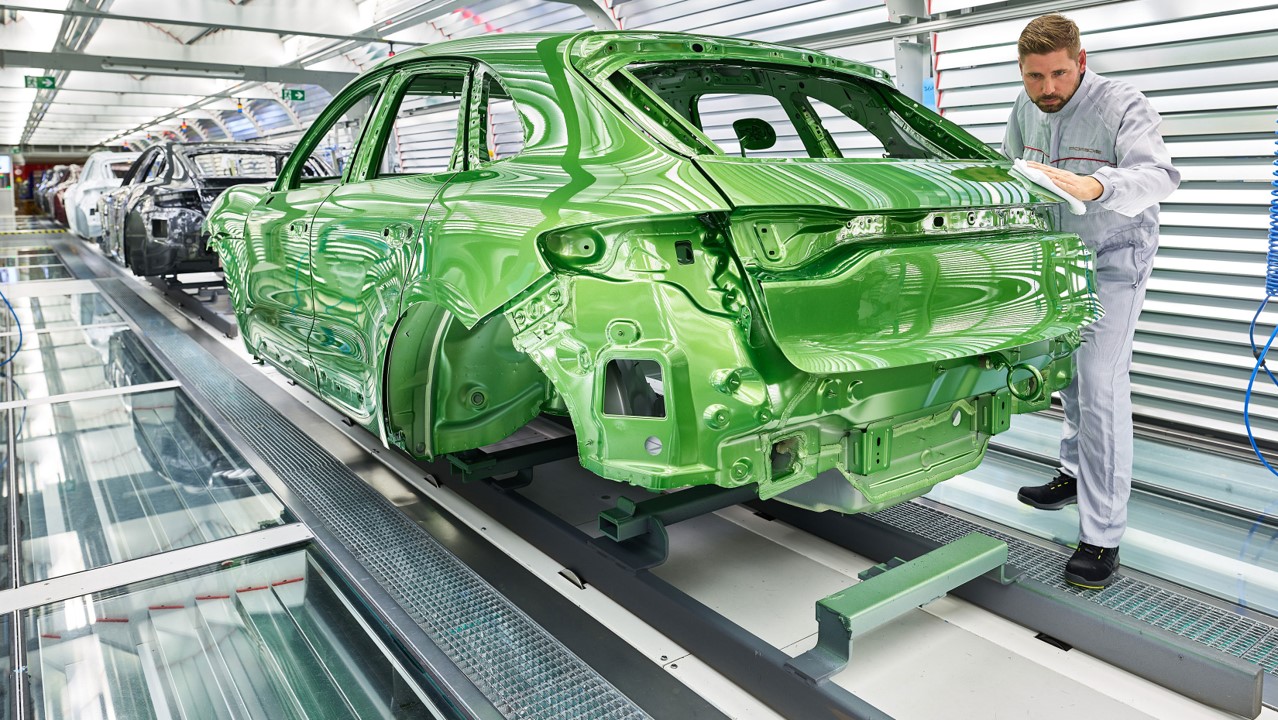
A German car manufacturer is already using paint_it to ensure that the quality of their body painting meets the required standards. By monitoring coat thickness, color, and appearance, the system can detect any defects in the paint and warn users with sufficient time to implement countermeasures.
In addition, the system’s ability to analyze trends can help to identify potential deficiencies before they occur, allowing the manufacturer to proactively take corrective action.
Explore more:
![[Translate to English:] [Translate to English:]](/fileadmin/_processed_/8/8/csm_Side_Header_ICS_WP_4242x1414_paint_it_8e4bc3d36d.png)
From brush to pixel
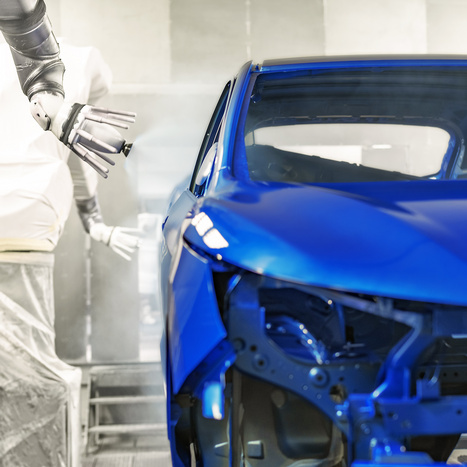
Next Level Painting
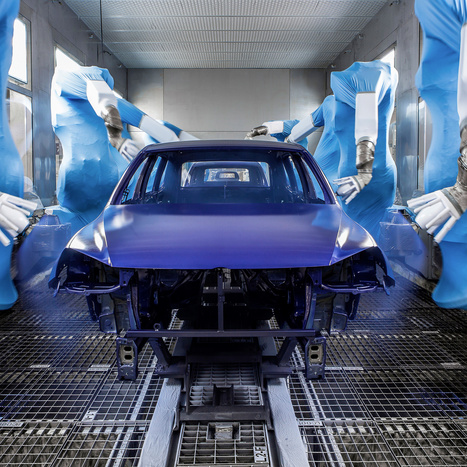