
Intelligent use of bolting process data
Increase your product quality and efficiency in manufacturing with the hidden potential in your bolting process data!
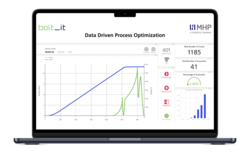
Our Customers
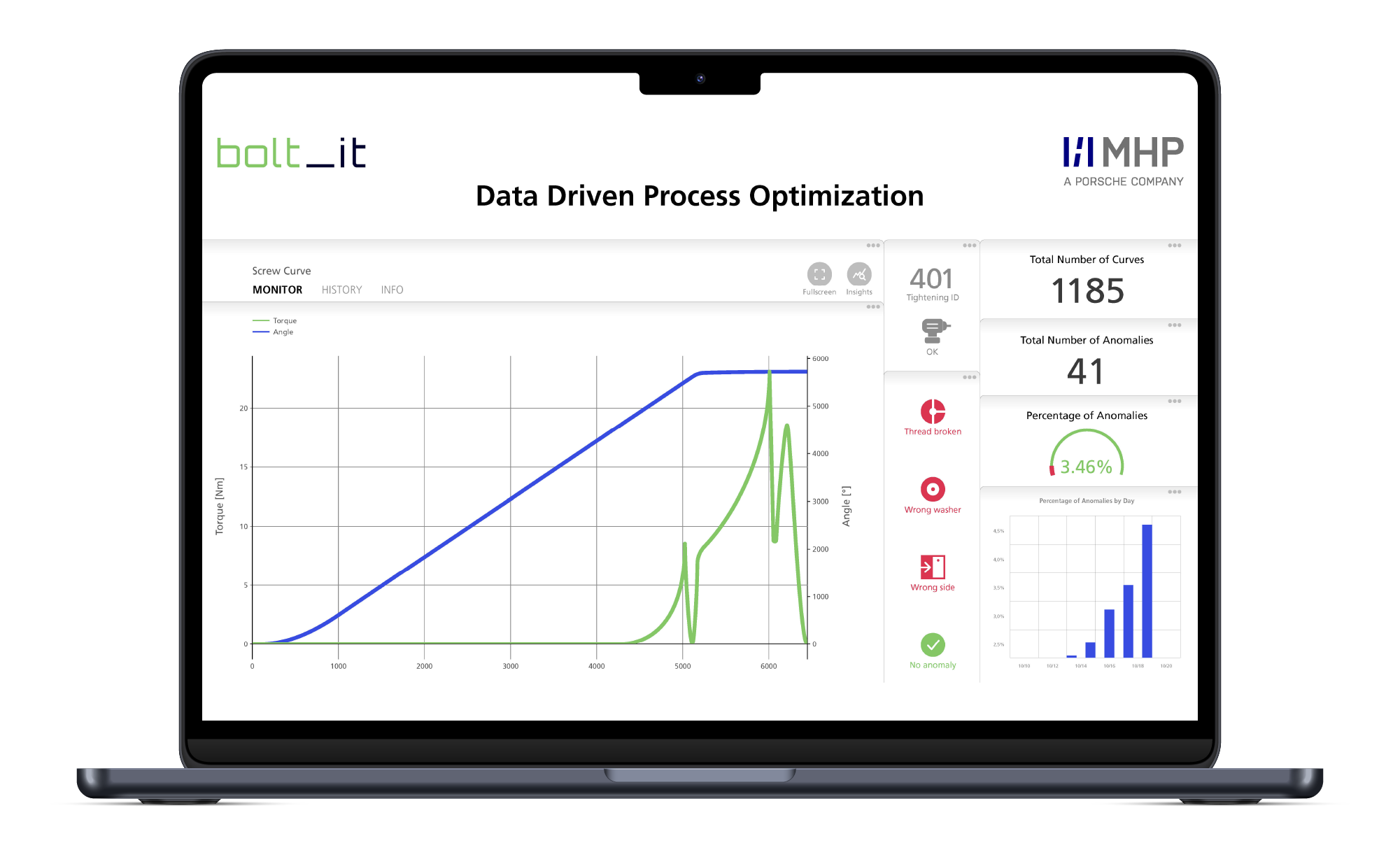
Make use of your bolting process data to its full potential with bolt_it
bolt_it kicks off where other software solutions finish:
This tool lets you discover, interpret and correlate previously undetected faults in your bolting process data.
In this way you implement previously unimagined optimization potential and increase your product quality sustainably.
Discover process anomalies early on
Thanks to bolt_it, you can identify unknown faults in the bolt connection as soon as they occur. Our software solution detects anomalies regardless of manufacturer or tool. This reduces the risk of product recalls and the associated effort and costs.
Significantly reduce rework costs
bolt_it provides specific recommendations to optimize your process parameters based on an analysis of your bolting data. It can help significantly reduce the necessary rework in troubleshooting and rectification and reduce your bolting process-induced rework costs by up to 70 per cent.
Significantly reduce response time
With bolt_it’s AI-based anomaly detection, you can quickly find out which parts of your product are affected by the faulty bolt connection. This allows you to detect products that need to be reworked in real time, and significantly reduce the output quantity that is generated by the time the fault is detected.
Key features at a glance
Intelligent analysis of bolting data
With bolt_it, you do not need to re-examine identical or similar situations.
Our AI-based software specifically supports the detection of error patterns and improves the monitoring and analysis of your process data, so that your experts can concentrate on the real work.
Cloud-based technology for a seamless knowledge transfer
bolt_it is linked to all your screwdrivers and feeds all bolting process data and analysis results directly into the cloud.
This means you and your quality engineers, plant employees and production line employees have access to all your bolting process data at all times.
Detect and visualize anomalies using AI models
Detect quality issues as they arise, such as faulty components or process fluctuations using AI models.
bolt_it increases your product quality and makes your production more efficient.
The five modules of bolt_it
With bolt_it, you can use your historical process data to draw conclusions about process and product improvements. For example, this module is good at checking specific past suspicions on a point-by-point basis. This will not only help you to find out how to prevent anomalies, but also optimize the development of new products.
Respond quickly to unknown faults directly in production with anomaly detection. bolt_it helps you prevent the same faults immediately, avoiding recall actions in emergency situations.
bolt_it saves you the manual effort of determining and limiting the best process parameters. Based on the analyzed bolting process data, the software provides you with regular or event-oriented recommendations, facilitating an optimal process at all times. Batch changes or temperature-related fluctuations in process results can therefore be more easily recorded and managed in a targeted way.
bolt_it helps you to classify potential faults or anomalies according to the severity of their impact on the product you produce. To do this, the AI alerts you as soon as a symptom occurs, analyzes the cause of the fault and suggests appropriate measures to remedy the problem. In accordance with the classification, the measures are displayed to the relevant responsible person in relation to the target group. In this way, the software controls which messages are displayed to production employees, process engineers or other parties involved and enables them to respond accordingly to the situation.
Optimize quality assurance processes using bolt_it trend analysis. This software monitors your process for systematic deviations, so you only need to examine samples to ensure your product quality.
bolt_it explained
Benefits
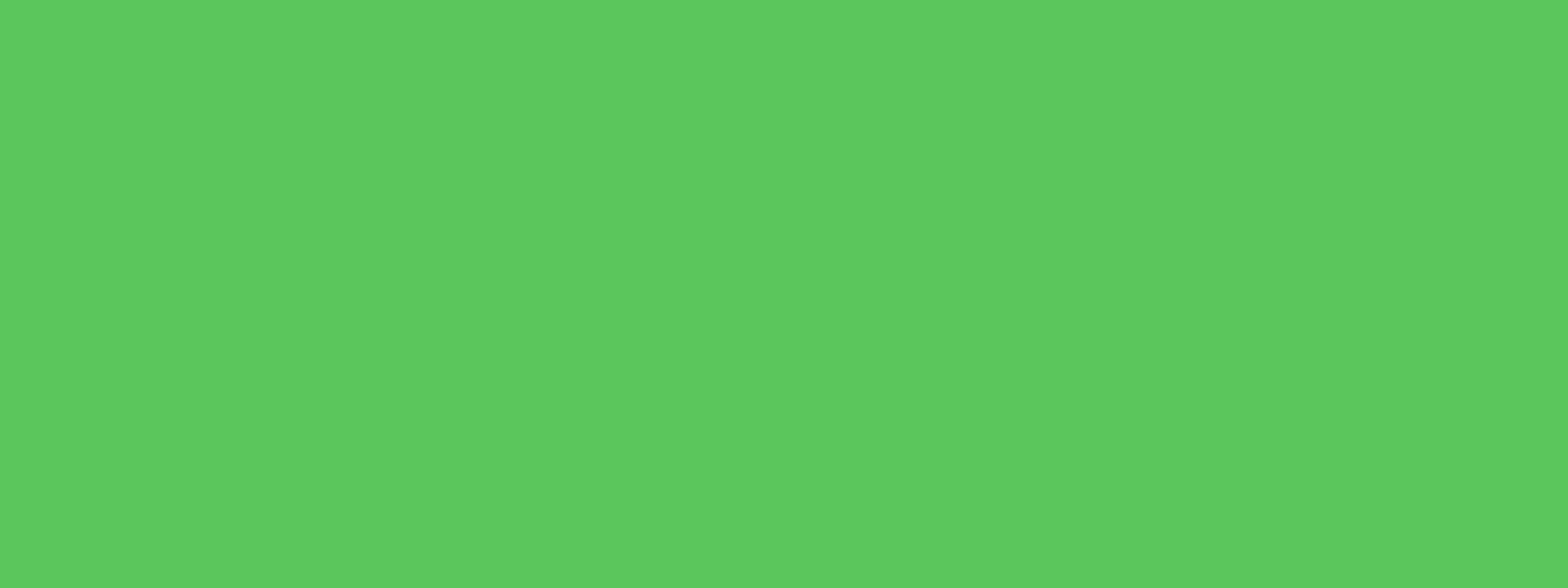
Customized and manufacturer-independent end-to-end solution
No matter what machines or bolts you use in your production, bolt_it can be used for all conventional industrial bolting tools! This one-stop-shop solution combines the data from your entire bolting process in one application, meaning you always have an overview.
Reduced workload
With bolt_it, you can reduce the amount of work that goes into your manual data analysis and parameter optimization by more than 90 minutes per week. In this way, you (indirectly) reduce your HPU (hours per unit). By supporting your employees in their work, AI enables you to accomplish more tasks with greater accuracy in the same time, which directly adds value to your business.
Faster decision-making
The standardized analysis and evaluation as well as the optimization suggestions from bolt_it allow you to make process-related decisions faster and enable you to produce more products in the same time, holistically increasing your production efficiency. According to industry experts, you can even increase your production capacity by one to two per cent annually with bolt_it.
How bolt_it has revolutionized anomaly detection at a large car manufacturer
Anomaly detection with bolt_it has already proven itself in the assembly line of a production plant of a big German car manufacturer. According to the manual analysis by process experts and the AI-based detection, 24 percent of the screwdriving curves classified as error-free showed anomalies that an early warning system can identify.
The developed algorithm was able to detect over 90 percent of these anomalies. The software solution also achieved consistently positive results in production at a major sports car manufacturer. Process anomalies were detected seven times more frequently on average compared to manual inspection methods.