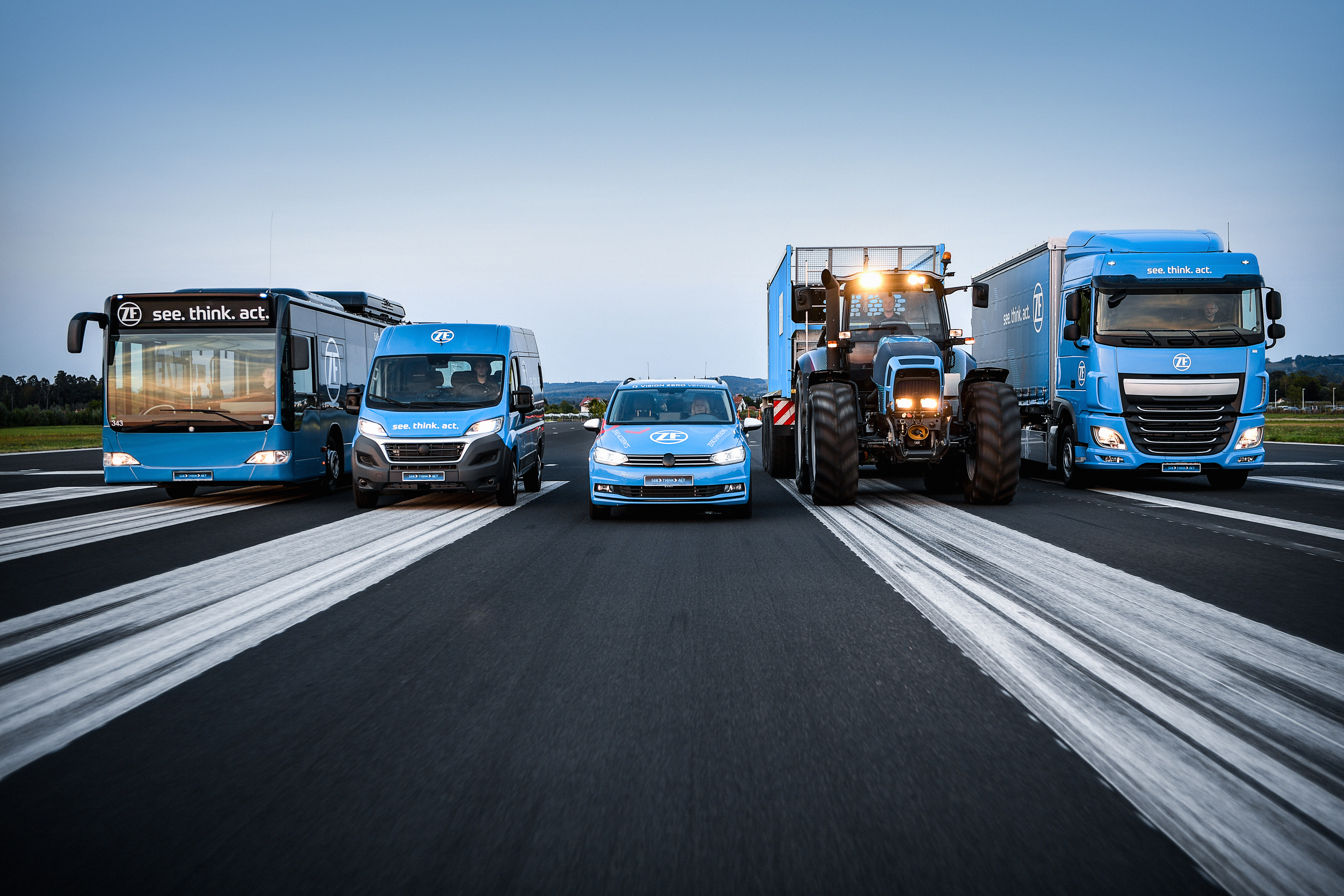
- Success Story
Successful IoT-Transformation in Product Development
Streamlining Global Product Development at ZF With a Centralized Measurement Data Platform.
For over a century, the global technology company ZF has been providing mobility solutions for personal transportation, automobiles, and industrial technology.
When creating new products, gathering data during the pre-development phase is crucial. However, in the past, this data hasn't always been collected centrally. This made it challenging for the company to find the datasets they needed. In some cases, it was even necessary to repeat tests on software-defined vehicles. To avoid these issues and enhance the product development process, the decision was made to develop a central IoT-enabled platform for measurement data.
In collaboration with doubleSlash as the development partner and MHP as the project coordinator and Product Owner, the new data management platform was successfully integrated into operational processes after a project duration of one and a half years.
An IoT (Internet of Things) platform is a type of digital infrastructure that connects, monitors, and controls various interconnected devices. It serves as an interface through which these devices exchange data and interact with one another. This enables users to efficiently manage their IoT devices and derive critical insights from the collected data.
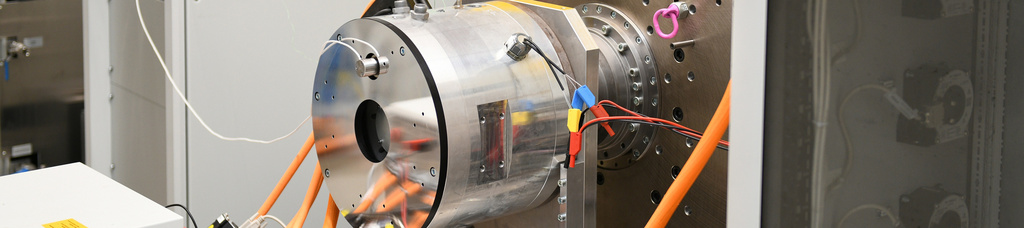
Three Parties, One Common Goal
ZF, doubleSlash, and MHP aimed to combine their strengths and realize a shared vision, which required a trusting collaboration.
Their objective was to ensure that essential information for product development – namely, measurement data – would no longer be lost during the development process.
They wanted to create a solution that would make it possible to query and automatically analyze this data.
Measurement data is essential data collected during the testing and validation phases of product development. It contains valuable information about the performance and functionality of the product under different conditions. By systematically collecting and analyzing the data, ZF can ensure the quality and reliability of the end product.
MHP as a partner for project and requirements management
Given the complexity of the project, it became evident that additional project management and process expertise would be required for tasks such as gathering and coordinating requirements, identifying stakeholders, and defining user stories. ZF chose MHP as their project partner based on MHP’s extensive knowledge of OEMs, suppliers, and manufacturing, as well as their ability to blend industry expertise with tailored solutions.
In its role as project coordinator, MHP not only collected and coordinated the multifaceted project requirements but also conducted technical assessments of the prerequisites. MHP also assumed the role of Product Owner. In this role, they demonstrated the ability to understand the needs of multiple departments and efficiently harmonize them with the development processes – both internally and with external teams. Their ability to record the requirements precisely and coordinate them seamlessly among all parties allowed MHP to effectively translate ZF's vision into reality, laying the groundwork for the project's success.
doubleSlash: The creative and technical engine behind the development of the IoT platform
doubleSlash has been one of ZF's strategic partners for many years. They design and operate innovative digital products for ZF, using their expertise to guide and execute the complete BizDevOps cycle.
Located in Friedrichshafen, doubleSlash and ZF have a history of close collaboration, which has resulted in holistic solutions that have been implemented across various areas of the company.

Challenges in Developing the Measurement Data Platform
As a technology leader with innovative digitalization approaches for software-defined vehicles, ZF has already developed partial solutions for an IoT and measurement data platform for use in various business areas. The aim now was to create a scalable platform that would be as open as possible, allowing other business areas to benefit from it as well.
ZF's previous solutions were analyzed and then integrated into the new platform. Making use of existing components in this way saved both time and cost.
When setting up the platform, it was essential to collaborate closely with multiple departments at ZF to ensure that their requirements could all be consolidated. During Scrum ceremonies, all departments received updates about progress and were able to give feedback. The teams worked with Azure DevOps, which made it possible to define tasks in relation to each other.
Team Spirit Leads to Success: The Birth of the IoT Platform
In a preliminary analysis, doubleSlash identified and evaluated ZF's systems and prepared to decide on a platform. During the initial phase, it was also important to identify all relevant interest groups and stakeholders and incorporate their needs and perspectives into the planning process. Requirements from different departments (personas) were recorded and divided into minimum viable products.
A minimum viable product (MVP) is a simplified version of a new product with only the most basic features. The purpose of an MVP is to gain insights into the target audience's needs and preferences with a minimal investment in effort. The strategy allows companies to develop products iteratively, on the basis of real user feedback. This reduces the risk of missteps during development.
Due to time constraints, doubleSlash designed the platform simultaneously. It was based on an IoT reference architecture and the prior analysis of core requirements for an IoT and data management platform. By defining user stories, they gained a clear understanding of how the end product should look and work from the user's perspective. These requirements influenced the details of the final product design and helped to define three MVPs. With the help of standardized templates, the stories were clearly depicted and documented.
From the start, the plan was to hand over all tasks to ZF's DevOps team. The goal was to empower the customer to independently operate the platform post-launch and continue developing the shared vision.
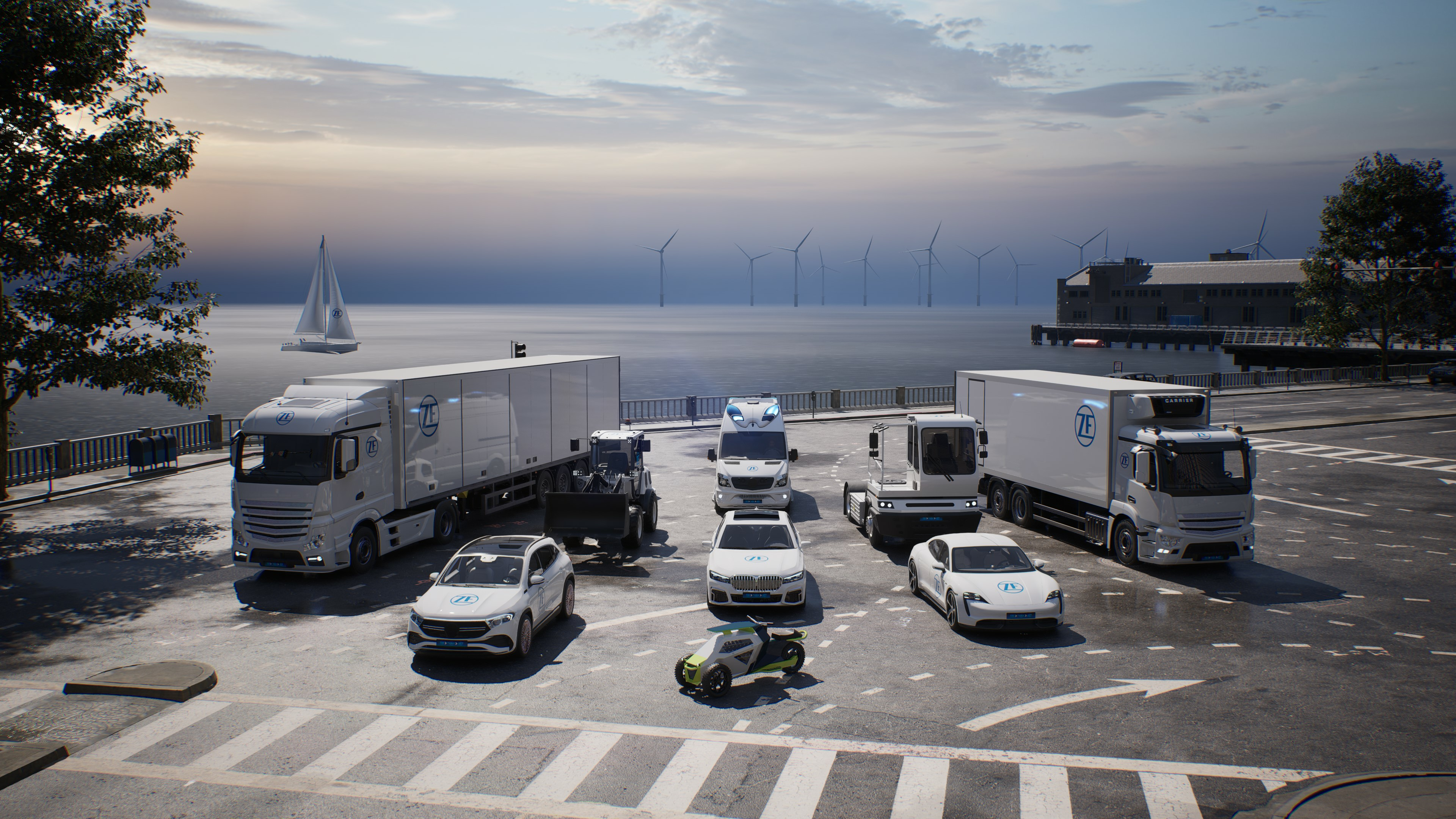
- Success Story
Cybersecurity and Lean Use of Cloud Technologies
A Platform for All Global Locations: From the outset, the application was designed to be highly automated and secure.
It was built using Azure standard components. In close collaboration with ZF’s IT security team, the application was thoroughly tested and the results of the security needs analysis and threat analysis were incorporated into the architecture and development.
Speeding up testing and validation: The solution was designed so that ZF could operate and expand it independently post-launch. ZF now has a central platform that is used across all global locations. Throughout the project, a team of ZF employees received training that would enable them to take over the platform and actively continue developing it. As Product Owner, Janos Vona coordinated the team's training and ensured that a timely handover was possible. doubleSlash made sure that the ZF team was actively involved in the development process using methods such as intense pair programming. This ensured a direct transfer of knowledge to the ZF team.
Thanks to MHP and doubleSlash's involvement, team members can now work independently on the development of the measurement platform without assistance from the other two parties.
This fulfilled a project requirement that had been important right from the start. The goal had always been to create a sustainable solution that ZF could operate independently after project completion, and which could be expanded piece by piece into other divisions.
With comprehensive knowledge transfer sessions at ZF headquarters, doubleSlash ensured that the ZF team had the technical and methodological know-how to continue developing and operating the platform.
Results, Facts, and Customer Feedback on ZF's IoT Platform
KPIs from a successful project
1000 global users
500+ connected test systems worldwide
200 connected test vehicles
Additional facts
The platform was nominated as the preferred Test Data Management platform for other ZF divisions.
Complete integration into ZF's security infrastructure
Sustainable use of existing infrastructure achieved by integrating ZF's Azure platform “OZEAN” and ZF's proprietary data logger “ProCV”
Sabine Rossbach, Project Manager at doubleSlash, was also enthusiastic: “Three partners, one team. During the collaboration, company boundaries were hardly noticeable. Everyone felt committed to the result and connected as partners.”
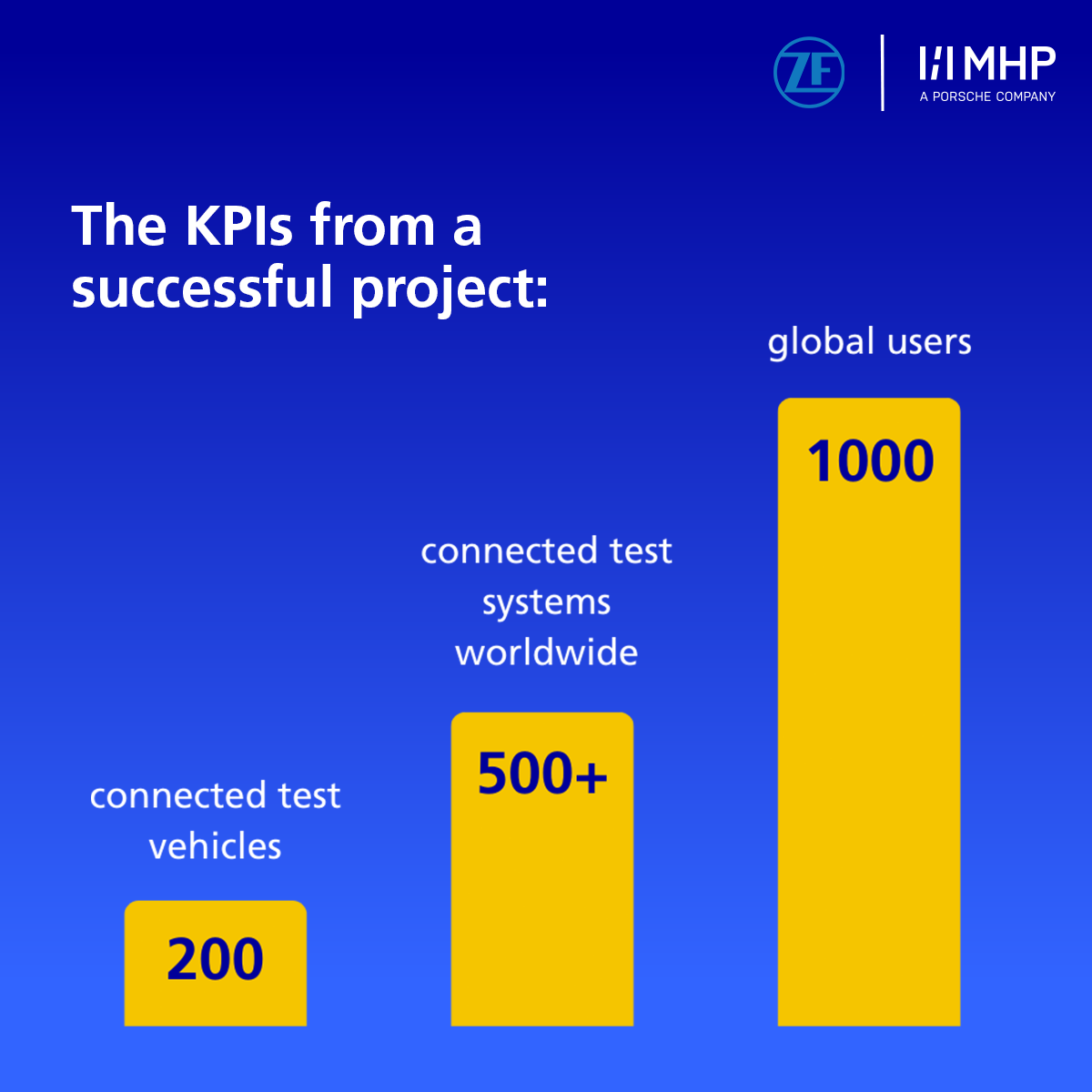
Laying the Foundation for Lean Validation: Using agile development to create the universally harmonized, user-friendly IoT platform resulted in two key benefits.
Not only has product development at ZF been digitized; development time has been reduced as well. The validation and simulation application with its reusable components laid the foundation for lean validation and actively supported the use of Digital Twins in development processes. The new measurement data platform allowed ZF to establish new processes for virtual validation, testing, and simulation.
And there are even more facts that highlight the positive impact of this new IoT platform:
Time savings and increased efficiency
- There is a standardized data format and metadata management.
- Data can be stored centrally and located quickly.
- Automated evaluation without manual effort is now possible.
- The global rollout saved time and resources.
Sustainability
- Thanks to the centralized and collaborative availability of test results, repeat testing due to misplaced data can be avoided.
Cost reduction
- Data storage is cost-effective and revision-proof (up to 20 years of revision security).
Centralization
- There is a global pool for harmonized and standardized data.
An Automated Cycle Revolutionizes ZF's Test Data Management
The IoT measurement data platform offers significant benefits for ZF’s product development, ensuring uniform test data and centralized access and simplifying the evaluation, comparison, and reuse of information. Employees can now reuse the results of analyses, which makes collaboration more efficient.
The digitization and automation of vehicle tests and validation will result in long-term cost savings, increased efficiency, and reduced effort, all of which will expedite market entry in the future. “The platform has laid the foundation for virtual validation and created a fully automated cycle for verification of testing data,” explains Janos Vona.
Dr. Alexander Graf, Head of Digitalization in the Electrified Powertrain Technology division
“With the new platform for our measurement data, we aimed to accelerate market entry while simultaneously reducing development costs and increasing quality. We achieved that. Having good partners with extensive experience on the project team during development and implementation was crucial to this success.”
Janos Vona, Head of IoT at MHP, took on the role of Product Owner in this project:
“As Product Owner, my focus was on enabling the project team to achieve rapid success by implementing MVPs, such as the connectivity of selected test vehicles and test systems. This helped us to win over the various departments and successfully integrate the platform into their daily testing processes. It was important to us to generate long-term value from the data. This included implementing a generic analysis interface, which accelerated the process of moving local testing software to the cloud. That made it possible to switch to fully automated cloud-based testing, as all necessary data was already in the measurement data platform.”