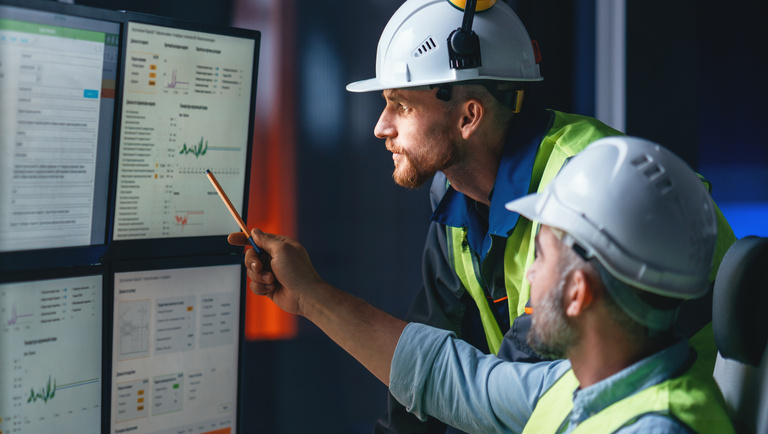
- Blog , Engineering & Production
- Published on: 24.10.2023
- 10:32 mins
Shift handover process: A digital dashboard for the production processes of the future
Perfectly calibrated machines and well-coordinated human workflows: safe, efficient production lines depend on productive process flows. To that end, production leads and their teams both benefit from an efficient, thoughtfully designed shift handover. For businesses in the manufacturing sector, a shift handover protocol can ensure the greatest possible transparency and make it easier for employees to have the right conversations. In addition, it ensures that relevant information goes directly to the responsible members of management.
Outdated shift handover templates and forms are standard in many companies
A shift logbook is essential for a seamless change of shifts. But how the logbook is implemented is a crucial factor — one that is often overlooked. In many facilities, outdated templates and checklists in the form of PDFs, PowerPoint presentations, old charts or paper lists are still being used to hand the shift off to the next shift lead. But these types of shift reports have a few disadvantages. They cause gaps in communication, lack quality and standardization, and are unsustainable and often unclear. All of that leads to disruptions in working processes: critical information is often passed on to decision-makers too late or not at all.
Challenges presented by outdated shift handover processes
Non-standardized, unstructured shift handovers are pain points that are familiar to many businesses in the manufacturing sector. As a result, a growing number of companies are opting to restructure their existing shift handover procedures and replace them with digital processes.
Here are a few more issues that awaken the desire for restructuring …
outdated, unknown or irrelevant performance indicators and production status.
no unified implementation of troubleshooting procedures.
no objective, comparative rating of effectiveness and profitability.
wasted effort due to outdated means of documentation.
no systematic record of the topics and decisions discussed in meetings.
prevalence of a silo mentality, which leads to a lack of transparency in reporting of key performance indicators and carrying out tasks
The time required to prepare the shift protocol can also be a deciding factor that makes a digital shift handover appeal to production staff. Tedious copying and pasting data from a variety of tools means that shift leads often spend up to two hours preparing the shift handover report.
Overly complex, unstructured or non-standardized checklists and templates, and outdated analog shift logbooks are the bane of many businesses in the manufacturing industry. Are you considering switching to a digital shift report? We would be happy to help. Feel free to get in touch with us to discuss the potential benefits of introducing a digital dashboard in your shift operations.
Use Cases: Innovative shop floor management for Porsche Leipzig GmbH
Digitalize the shift handover to increase efficiency— that was the goal of Porsche Leipzig GmbH in 2022, when they worked with MHP to introduce a digital dashboard for shift handovers.
Use Cases: Innovative shop floor management for Porsche Leipzig GmbH
More than just a standardized checklist: MHP’s goal was to develop a digital dashboard that would provide added value for the company by serving as a central information platform for Porsche Leipzig GmbH.
Project stakeholders made it their goal to improve the flow of communication across shifts. This was done by standardizing and structuring the collection and display of current performance indicators, relevant data and any disturbances that might arise. In addition, they wanted to unify the exchange of information and standardize procedures for reporting events that occurred during the shift. Implementing these reporting procedures along with a software-supported shift handover would make it possible to compare key performance indicators as well as to identify optimization potential in the future. It would also help to minimize error and risk.
For that to happen, it was essential to be well-acquainted with the procedures and events during the shifts, as well as the working procedures followed by the employees on the shopfloor. It's also important not to alter them or interfere with the way they were carried out. To achieve the core goal of the shift handover digitalization project, the MHP team placed great value on making shift operations as frictionless as possible.
The solution would need to offer a variety of options and wide range of features, but also be designed for cost efficiency in terms of required resources. To guarantee resource efficiency, ease of use and individuality in equal measures, existing tools that were already in use at Porsche Leipzig GmbH were incorporated into the dashboard development.
An overview of the framework used for development of the digital dashboard
Goal:
- Introduction of a digital shift handover process
Process demands:
Incorporating established tools during the development process
Leave employee procedures unchanged to the greatest extent possible
Integration into the existing production IT system
The benefits of a digital shift handover protocol
A digital protocol for shift handover and documentation of events during the shift holds great potential for manufacturing companies. The approach designed by our project team for Porsche Leipzig GmbH can be scaled for use in other sectors or other companies from the automotive industry that face similar challenges.
Here are some of the ways that the dashboard developed by MHP can benefit your business:
Real-time communication between employees: Information can be entered into the system immediately and shared with relevant team members. This speeds the flow of information and allows employees to react quickly to events or problems.
Centralized documentation: A digital shift logbook allows you to save all relevant data, protocols, and documents in a single location and make them easily available to authorized users. This simplifies the search for information and saves time that would otherwise be spent digging through paper documents or various files.
Integration with systems currently used within the company: Data from production systems or other digital platforms can be imported and linked into the digital shift logbook. This creates a seamless connection between the various systems and allows for a holistic overview of your production processes.
Improved transparency and cooperation: Because all relevant information is available to all team members, communication, and collaboration across the various shifts improves significantly. This simplifies coordination, knowledge sharing and collaborative problem-solving – even in cooperation with other shifts.
More sustainable processes: Documentation using the digital shift handover process also helps to reduce CO2 emissions. Eliminating paper documents and using electronic archives helps to save resources and reduce environmental impact. In addition, opportunities to optimize and save emissions can be identified more quickly using digital documentation. This reduces emissions in the long term.
Easy to use and very user-friendly: The design of the digital shift report’s user interface lets staff use the app intuitively, without extensive training. This makes the program extremely versatile and effective, so that you can use the digital shift handover to your full advantage.
Standardization for maximum reliability: The digital shift report also serves as a “single source of truth” — the one place your employees can look to for any protocol or piece of information that they need. This reduces misunderstandings, miscommunication, and errors, because all stakeholders have access to the same information and are on the same page.
Overall, the digital shift handover process improves efficiency, quality, and sustainability in production and helps to optimize working processes.
Would you like to make a digital shift handover possible in your company? Please get in touch with us for a consultation.
4 steps to implementing a shift handover procedure
MHP designs your digital shift logbook to meet the unique needs and demands of your business, so you can enjoy the benefits of a digital dashboard. This is how our process works:
- Step 1: Analysis
In the first phase, we carry out a detailed analysis of data and processes. We examine the existing templates and tools that are being used for the shift handover process, then identify the required data sources. This information is used to determine the technical requirements for the dashboard app. Consequently, this analysis forms the basis for the design of the digital shift handover protocol. It ensures that the finished app allows you to collect all the relevant information and use it effectively. - Step 2: Building an infrastructure
After the data and process analyses are completed, we establish the tool ecosystem for your digital dashboard. MHP chooses software solutions that meet your company’s unique needs. In making their choices, our experts ensure that your dashboard is adaptable and capable of integrating a variety of data sources. The tool ecosystem is developed so that real-time data, key production figures and other relevant information can be displayed at a glance. - Step 3: App development begins
The next step is the actual development of your app. During the entire process, we work closely with both the production leads and the production staff to identify the needs and demands within the shift operations. When designing the app, we place the utmost priority on user-friendliness and make sure that users can navigate quickly and use the app with ease. This applies to both entering data and sharing that information. - Step 4: Testing functionality
After the dashboard app is developed, it’s time for the test phase. Groups of employees and team leads are given the opportunity to test the app to see how well it meets their needs in practice. This allows us to identify any areas that still need to be adjusted and improved. Feedback from employees is also incorporated as we fine-tune the programming.
This four-step approach allows MHP to seamlessly implement the digital shift handover process. The in-depth analysis of data and processes lays the foundation for the design of the digital shift handover process, while the tool ecosystem and the intuitive dashboard app allow data to be visualized and used effectively. The test phase with multiple stakeholders ensures that the app can be continuously improved to meet the needs and demands of employees. MHP places great value on cooperation with the production employees; this helps us to achieve an optimum integration of the digital shift handover process into the company’s business processes.
Optimize your shift changes with a digital protocol
The manufacturing of the future will no longer rely on outdated templates and shift logbooks. A digital shift handover protocol holds great potential for manufacturing companies: it can improve both collaboration and sustainability. The approach is scalable and can be used in other sectors as well as in other types of manufacturing companies facing similar challenges to Porsche Leipzig GmbH.
The finished app can easily be used in other production areas with minimal effort. With the digital shift handover procedure, companies can optimize their work processes, improve efficiency and reduce their environmental impact at the same time. This makes the digital dashboard a future-oriented solution for shift handovers—and perhaps for your company, as well.
Rely on the expertise of our MHP consultants and enjoy the wide range of benefits offered by a digital shift handover process.
Common questions about a digital shift handover process
A digital dashboard in the form of an app is particularly helpful for introducing standardized logic in the shift handover. It collects all relevant information in a central location, so the responsible parties can be informed about any incidents or irregularities directly during the shift handover. To create it, you can build on the experience of an expert team of consultants who will create and integrate the standardized logic in close consultation with the responsible stakeholders—all while making use of your existing tools and processes.
Production leads benefits from a digital shift handover not only because information can be shared clearly and transparently, but also because they receive information from each shift immediately, without delay. This helps to identify production errors, disturbances, and opportunities for optimization early on. In addition, a digital shift report gives production leads a central overview of key relevant statistics. They benefit from this centrally stored data, which they can use as the basis for important decisions.
Use of a digital shift handover not only improves your company’s profitability—it also improves communication and cooperation throughout the production team. Production teams experience a stronger sense of unity, because they are able to communicate more transparently and work together to solve problems—even across different shifts.
Ensure that all users are shown how to work with the digital shift handover application. Inform your production and shift leads that all important information, problems, and statistics must be entered directly into the shift report, and use the information gained in this way to regularly update your processes. Just like your company, the digital dashboard is constantly changing. It is essential that you pay attention to regular updates and add any relevant new data, statistics, etc. to the system. You should also incorporate feedback from the production team members.
Members of the production team should be incorporated into the process from the very beginning. Make clear the benefits of a digital shift report—such as more transparency or an improved flow of information. When implementing a digital dashboard, you should also invite your employees to share their user feedback during the testing phase, and that feedback should be incorporated into final app design. In addition, you should ensure that production processes can continue as usual during the integration of the digital shift handover report.